How long does it take to produce custom paper box packaging samples and mass orders? | Winpack Expert Guide
- How Long Does It Take to Produce Custom Paper Box Packaging Samples and Mass Orders?
- What Factors Influence Production Time for Custom Paper Box Packaging?
- What Are the Typical Minimum Order Quantities (MOQs) for Custom Packaging?
- How Can Businesses Reduce Lead Times for Custom Packaging Orders?
- Are There Sustainable Options for Custom Paper Box Packaging?
- What Should Businesses Consider When Choosing a Custom Packaging Supplier?
How Long Does It Take to Produce Custom Paper Box Packaging Samples and Mass Orders?
In the custom paper box packaging industry, production timelines are a critical concern for businesses looking to procure branded or specialized packaging solutions. Whether you're a small business owner, e-commerce retailer, or large-scale manufacturer, understanding the time required for producing samples and mass orders can help streamline your supply chain and meet market demands. Generally, sample production for custom paper boxes takes between 3 to 7 days, depending on design complexity and supplier capabilities. Mass orders, on the other hand, can take anywhere from 2 to 6 weeks, influenced by order volume, material availability, and production capacity. These timelines are based on industry insights and may vary depending on specific vendor processes or market conditions in 2025, as the global paper packaging market continues to grow, valued at USD 417.31 billion in 2025 with a projected CAGR of 4.68% through 2030 (source: Mordor Intelligence).
In this blog, we’ll address the primary question of production timelines while exploring other common concerns and热门 questions that users often have when procuring custom packaging solutions. Let’s dive into the top 5 questions related to this topic.
What Factors Influence Production Time for Custom Paper Box Packaging?
Several factors can affect the lead time for both samples and mass orders of custom paper boxes. These include design intricacy (e.g., custom printing, embossing, or die-cutting), material sourcing (specialty paper or sustainable options may require longer lead times), and the supplier’s production capacity. For instance, during peak seasons, such as holidays, production schedules may be delayed due to high demand. Additionally, geographic location plays a role—local suppliers may offer faster turnaround compared to international ones due to shipping times. Communication and approval processes for designs also add to the timeline, as revisions can extend sample production by a few days.
What Are the Typical Minimum Order Quantities (MOQs) for Custom Packaging?
Minimum Order Quantities (MOQs) are a common concern for businesses, especially small enterprises or startups. MOQs for custom paper box packaging often range from 500 to 1,000 units for mass orders, depending on the supplier and the complexity of the design. Smaller runs may be possible with digital printing technologies, but they often come at a higher cost per unit. For samples, suppliers typically produce 1 to 5 units to allow for testing and approval before full-scale production. Understanding MOQs helps businesses plan inventory and budget effectively while avoiding overstocking or underordering.
How Can Businesses Reduce Lead Times for Custom Packaging Orders?
To expedite production, businesses can take several proactive steps. First, finalize designs and provide clear specifications to suppliers to minimize revisions. Second, choose readily available materials rather than niche or imported options to avoid delays in sourcing. Third, partnering with a reliable supplier with in-house design and production capabilities can significantly cut down on lead times. Lastly, placing orders during off-peak seasons or planning well in advance can help avoid bottlenecks. Efficient communication and early approvals are key to meeting tight deadlines.
Are There Sustainable Options for Custom Paper Box Packaging?
Sustainability is a growing priority in the packaging industry, driven by consumer demand and regulatory pressures. The paper and paperboard packaging market is projected to grow from USD 323.78 billion in 2024 to USD 492.33 billion by 2034, with a focus on biodegradable and recyclable materials (source: Towards Packaging). Many suppliers now offer eco-friendly options like recycled paper, FSC-certified materials, and soy-based inks. While sustainable materials may sometimes extend production timelines due to limited availability, the long-term benefits of aligning with green practices often outweigh minor delays.
What Should Businesses Consider When Choosing a Custom Packaging Supplier?
Selecting the right supplier is crucial for ensuring timely delivery and quality. Businesses should evaluate a supplier’s production capacity, experience in the industry, and ability to handle custom designs. Checking reviews, requesting samples, and verifying certifications (like ISO or sustainability credentials) can provide insight into reliability. Additionally, consider the supplier’s location and shipping policies to account for potential delays. A transparent supplier with strong customer support can make the procurement process smoother and more efficient.
In conclusion, understanding production timelines and addressing related concerns can empower businesses to make informed decisions when procuring custom paper box packaging. At Winpack, we pride ourselves on being a trusted partner in the packaging industry, offering fast turnaround times, flexible MOQs, and sustainable options tailored to your needs. Our state-of-the-art facilities and dedicated team ensure that both sample and mass orders are delivered with precision and efficiency, helping Winpack stand out in a competitive market. Contact Winpack today to experience unparalleled service and quality in custom packaging solutions.
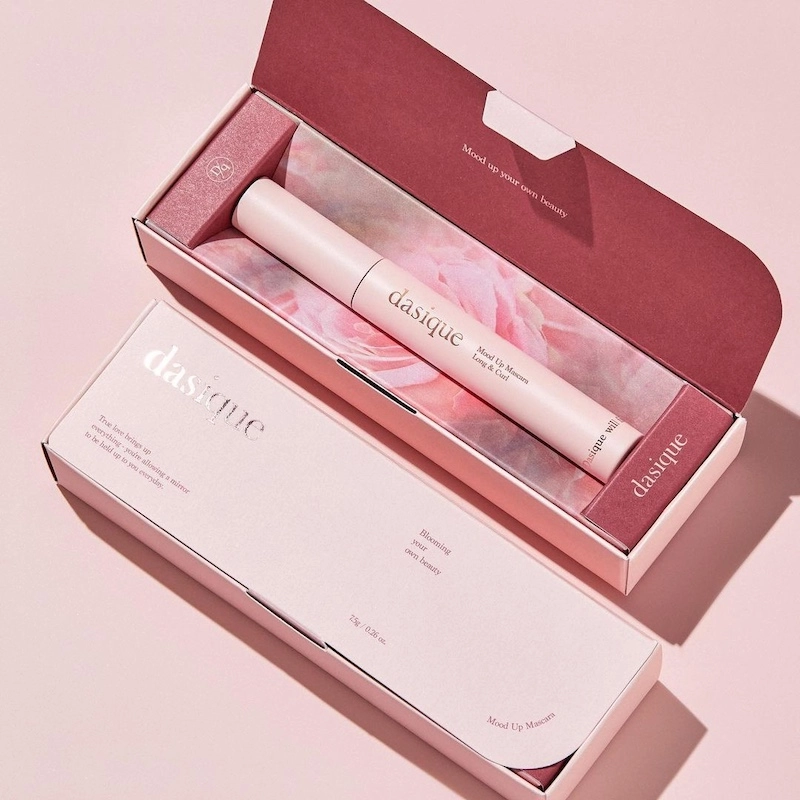
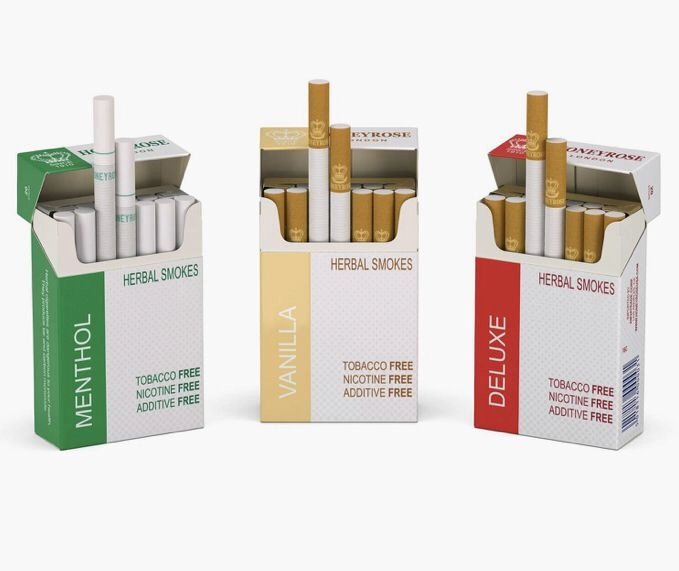
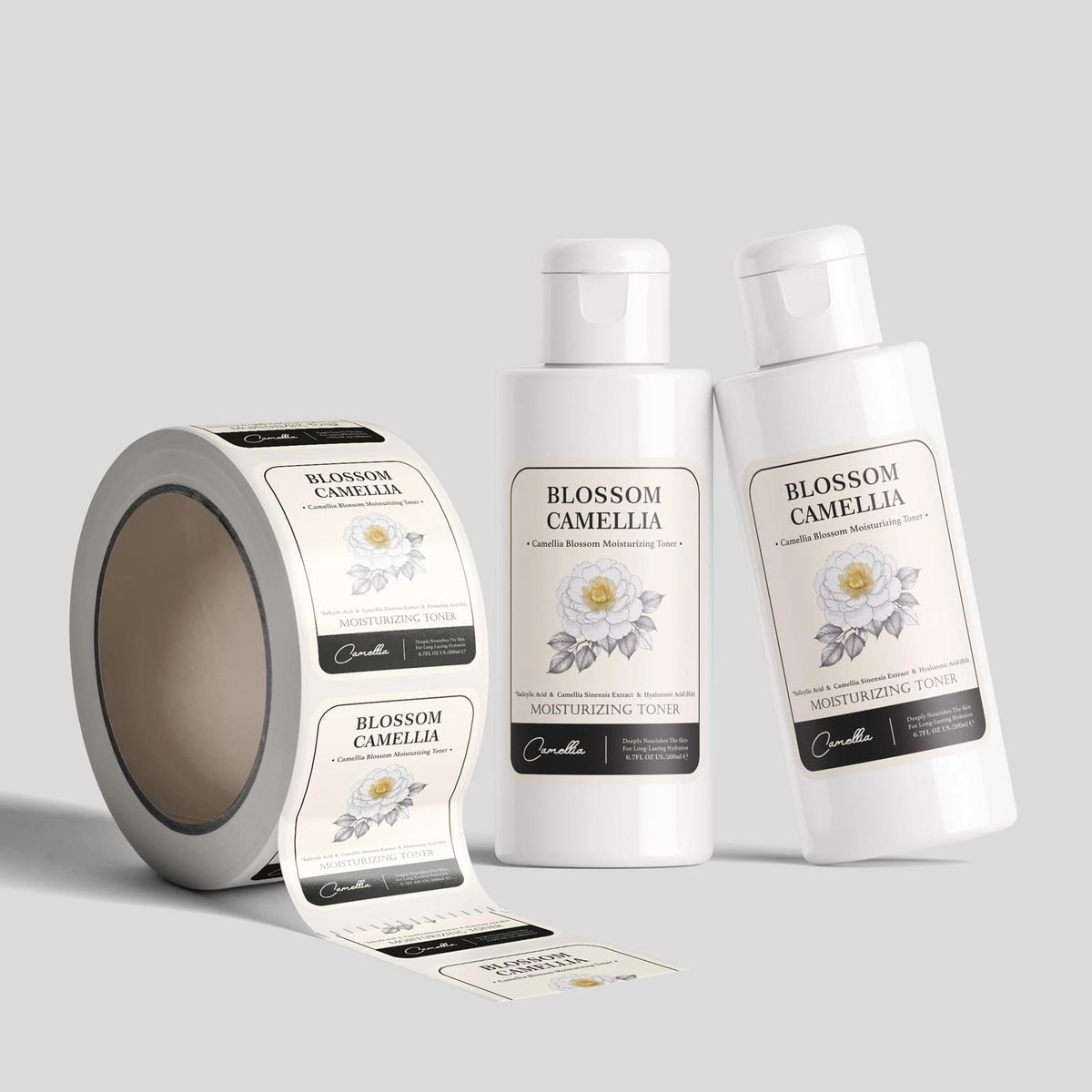
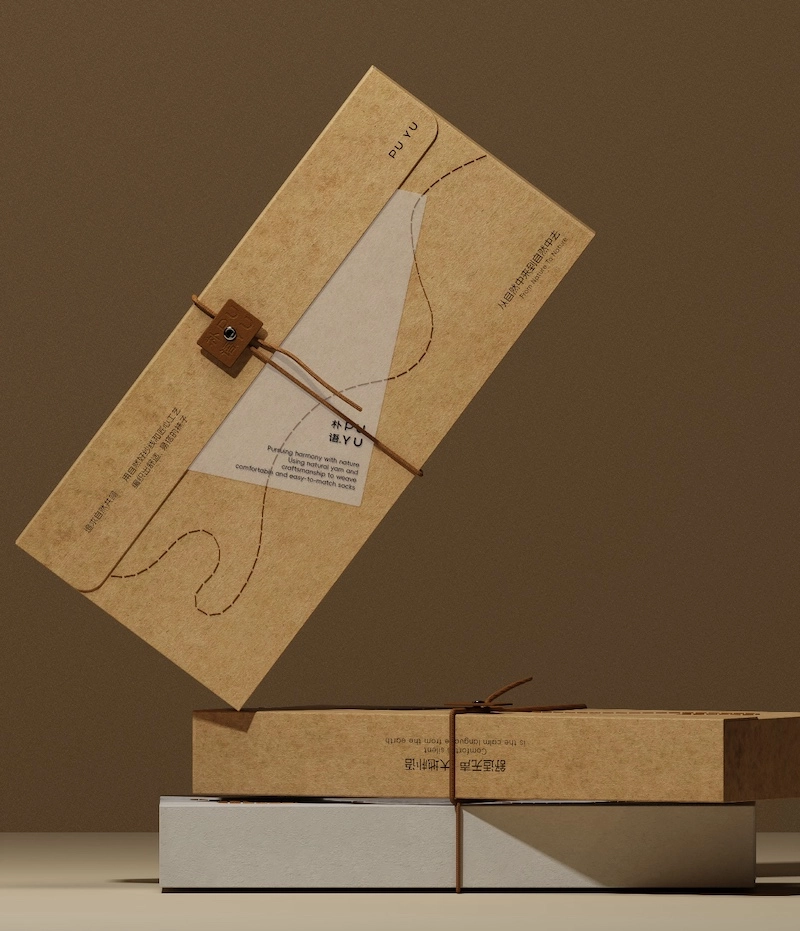
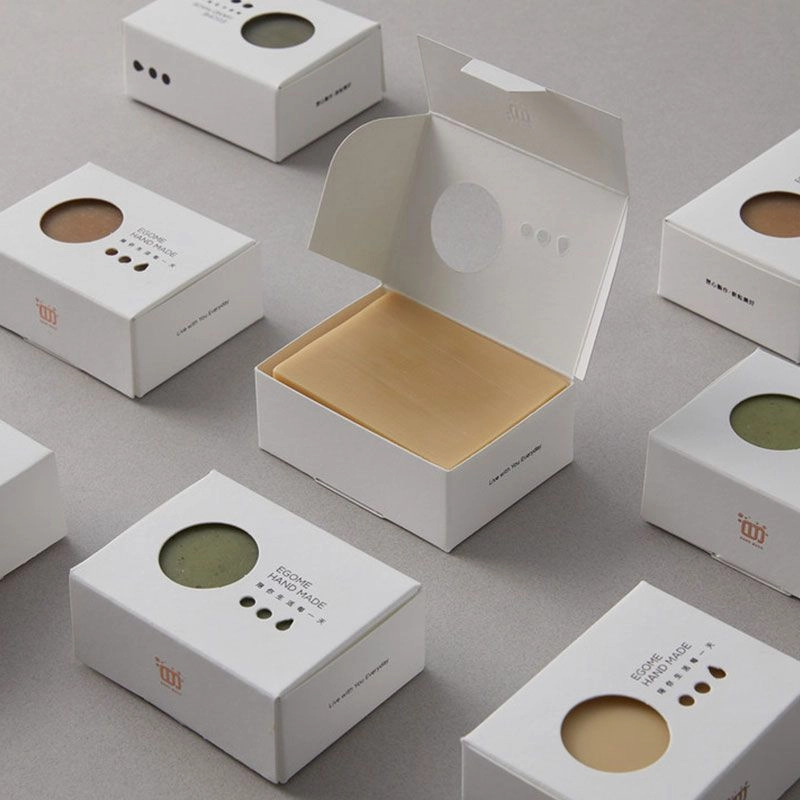
About Us
How long does shipping take?
Air freight options range from 7-21 days, while ocean freight options range from 26-71 days. If you need some units expedited earlier, consider splitting your shipment between air and ocean!
Can you do the design for us?
Yes. We can offer free design the artwork according to your requirement.
OEM Services
What quality control measures do you have in place?
We implement strict quality control throughout our production process, including:
ISO-certified quality management systems
pressSIGN color management for consistent printing quality
ERP production tracking for precision and efficiency
Rigorous inspections at every stage of production
Rigid Drawer Box
How long does it usually take from design confirmation to delivery?
The lead time is usually 15-25 days, depending on the production of the order
About Printing Craftsmanship
What are the different types of printing techniques?
There are various printing techniques used for different purposes, including:
Offset Printing – Ideal for high-volume commercial printing, offering sharp and high-quality images.
Digital Printing – Suitable for short-run printing with fast turnaround times.
Screen Printing – Used for printing on textiles, plastics, and other materials with thick ink layers.
Hot Stamping – Adds metallic or pigmented foil using heat and pressure for a luxurious look.
Embossing & Debossing – Creates raised or recessed designs for a textured effect.
UV Printing – Uses ultraviolet light to instantly dry ink, offering vibrant colors and enhanced durability.


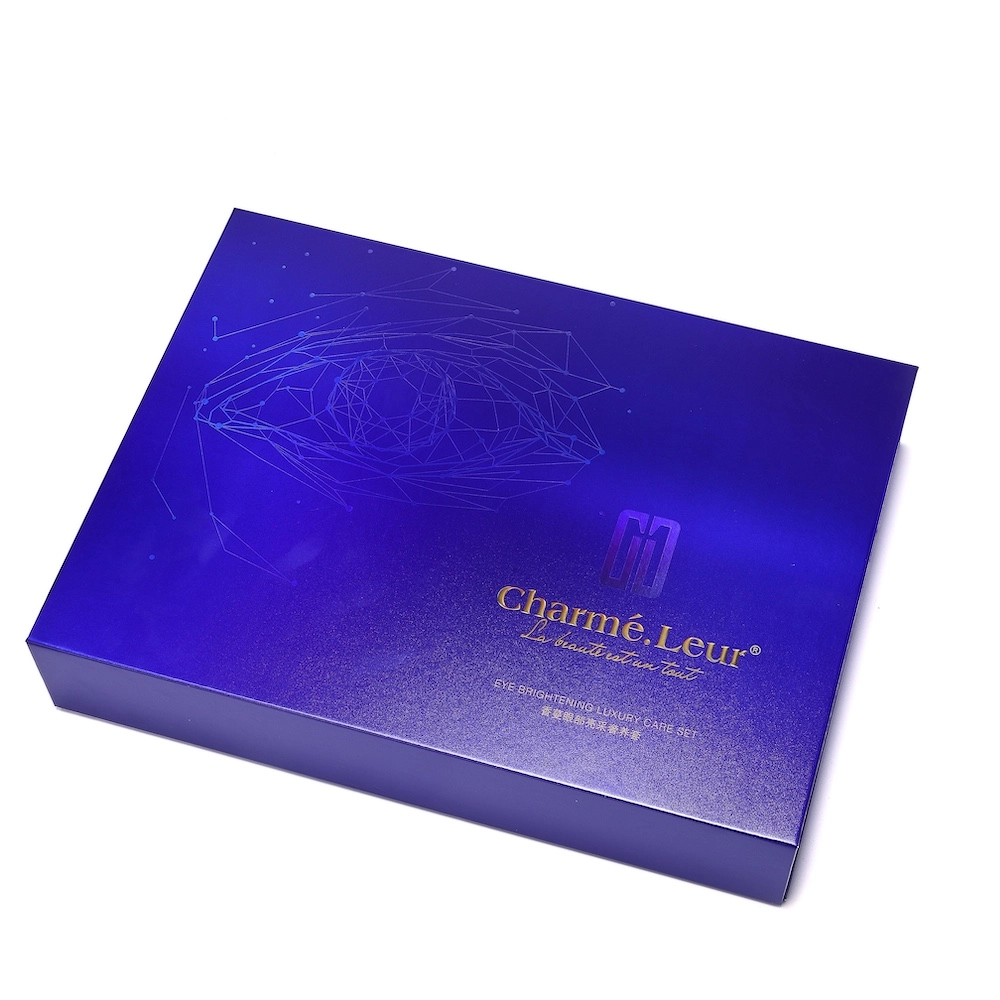

Start Your Packaging Journey Today
Discover Our Curated Collection of Bespoke Packaging Cases & Tailored System Solutions
© 2025 WINPACK PRINTING. All rights reserved
Wenhua Printing packaging
winpackprinting
Winpack Printing