How Does a High-Quality Gift Box Come Into Being? Take You Into the Winpack Factory
In a world where packaging is more than just a container—it’s a brand statement—a high-quality gift box can elevate your product, captivate your customers, and add undeniable value to your brand. But have you ever wondered how such a premium gift box is made? At Winpack Printing, we take pride in transforming creative ideas into beautifully crafted packaging. Let us take you behind the scenes into our factory and show you how it all happens.
Step 1: Understanding the Brand and the Product
Every gift box project starts with one essential step: listening to the client. We dive deep into your brand’s identity, the product’s characteristics, and the message you want to convey. Whether it’s for cosmetics, chocolates, electronics, or luxury goods, the packaging must align with your market and audience.
Our design and sales team work closely with you to develop concepts, materials, structures, and finishes that reflect your vision—while staying practical and cost-efficient.
Step 2: Custom Structural Design & Sampling
Next comes structural design. Our experienced engineers use CAD software to design the box die-cut layout, ensuring perfect fit and durability.
We then produce a physical sample (prototype) using your selected materials, which allows you to feel the texture, test the structure, and evaluate the colors and finishes in real life. This crucial stage helps fine-tune all the details before mass production begins.
Step 3: Material Selection
A great gift box starts with great materials. At Winpack, we source premium paperboard, specialty paper, greyboard, and eco-friendly materials based on your needs.
Whether you want a smooth matte surface, a luxurious embossed pattern, or a natural kraft feel, we ensure the materials match your brand’s aesthetics and sustainability values.
Step 4: Printing with Precision
Once the design is finalized, it’s time to bring it to life with high-quality printing. Our Heidelberg and Komori offset printing machines deliver sharp, vibrant, and color-accurate results.
We also offer a wide range of special finishes to add that “wow” factor:
Hot stamping (gold, silver, holographic)
Spot UV coating
Embossing / debossing
Soft-touch lamination
Each finish is carefully applied to highlight key design elements and enhance the tactile experience.
Step 5: Die Cutting, Gluing & Assembling
After printing, sheets are die-cut into the box shape using precision molds. The cut parts are then glued and assembled—manually or by machine—depending on the box type.
Our skilled workers ensure that every fold is crisp, every edge is clean, and every box meets our high standards. For complex rigid boxes, we also use automated box-wrapping machines to ensure consistent quality and speed.
Step 6: Rigorous Quality Control
Quality is not an afterthought—it’s at the heart of everything we do. At each production stage, our QC team performs thorough inspections, checking for color accuracy, surface defects, structural integrity, and finishing quality.
Only boxes that pass our strict criteria move on to packing and delivery.
Step 7: Packaging and Worldwide Shipping
Finally, your boxes are packed with care—whether flat-packed or pre-assembled—and prepared for safe shipping. We work with trusted logistics partners to deliver your packaging on time, whether it’s to local warehouses or international destinations.
Why Choose Winpack Printing?
At Winpack, we don’t just manufacture boxes—we build packaging experiences. With over a decade of experience, a dedicated in-house team, and cutting-edge equipment, we are trusted by brands worldwide for:
Full customization from concept to delivery
Competitive pricing with no compromise on quality
Fast sampling and reliable lead times
Strict quality control at every step
Eco-conscious solutions and materials
Ready to Create Your Next Gift Box?
Let’s work together to design packaging that tells your story and impresses your customers. Contact us today to get started.
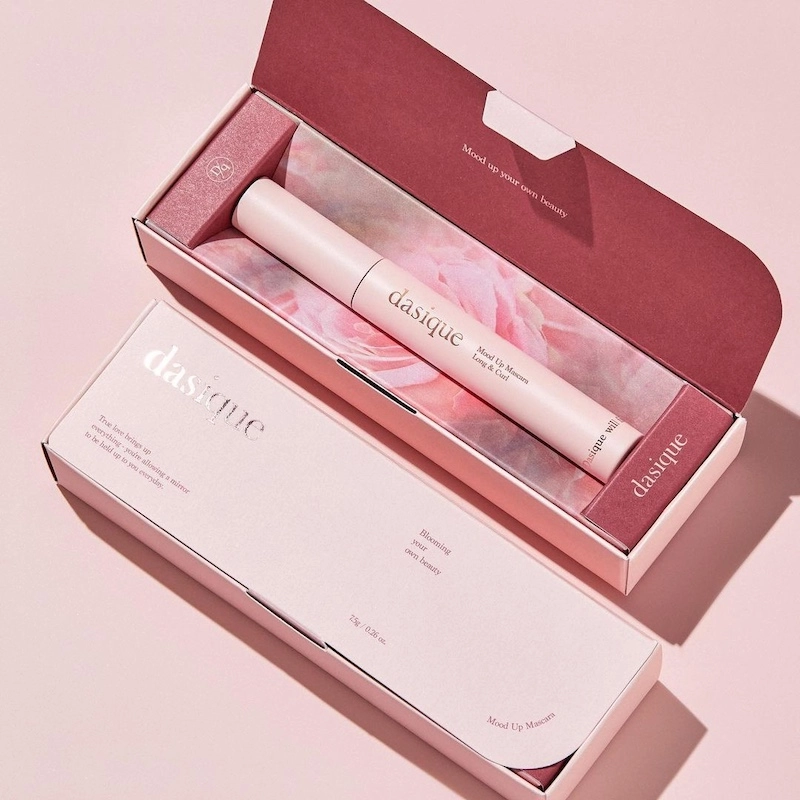
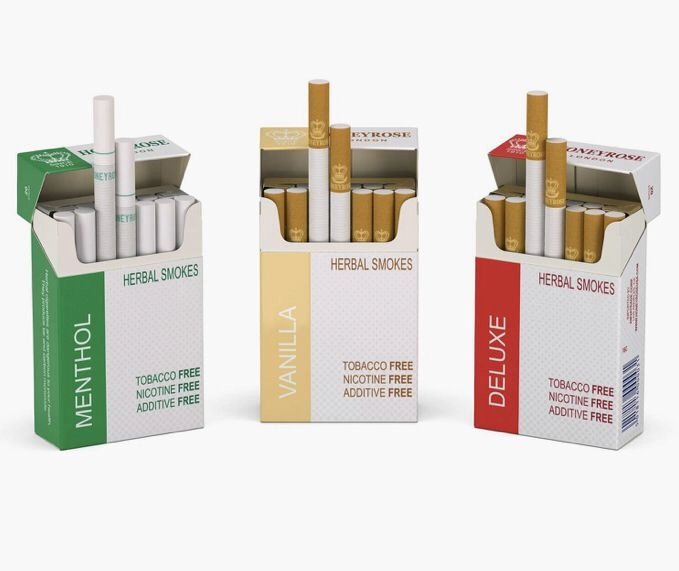
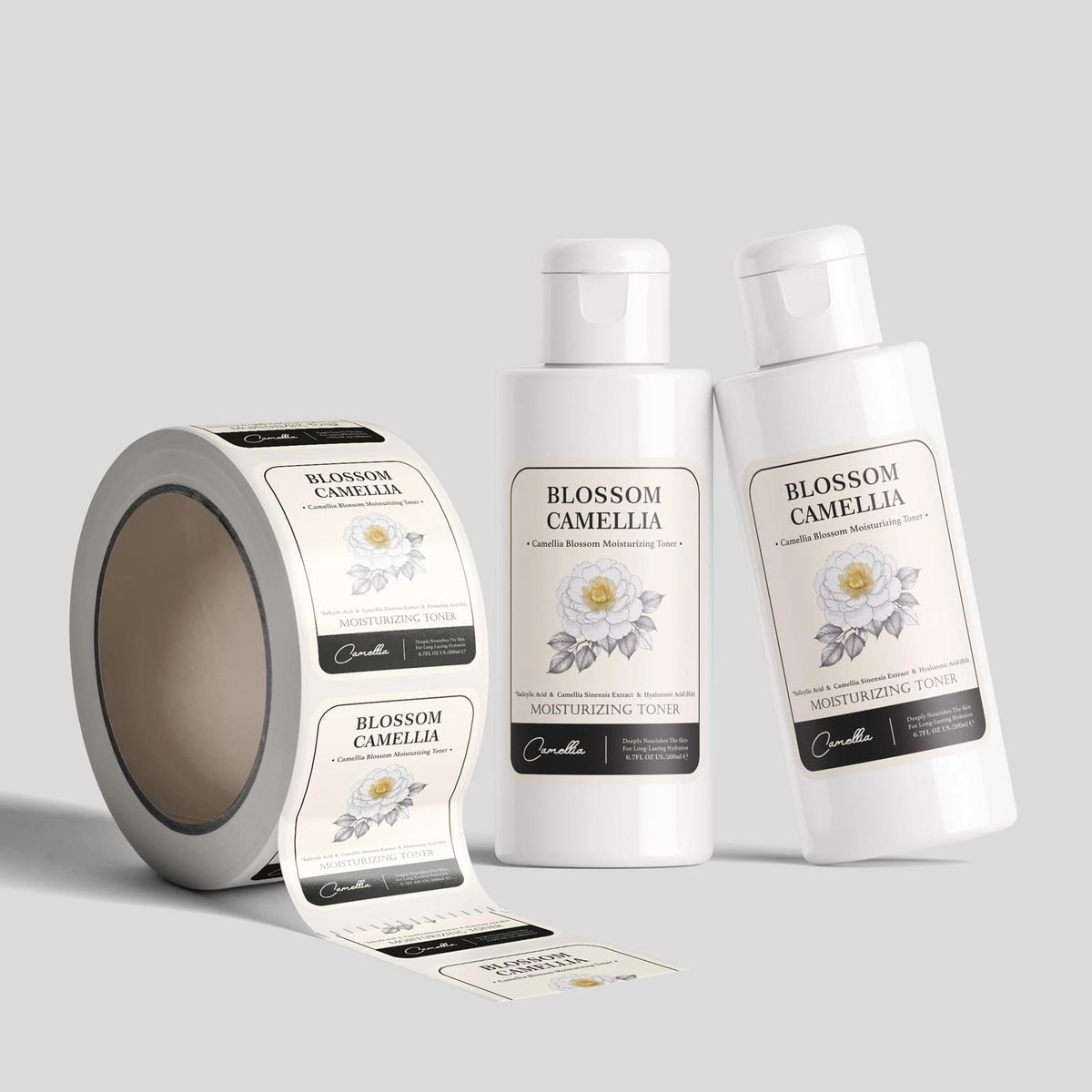
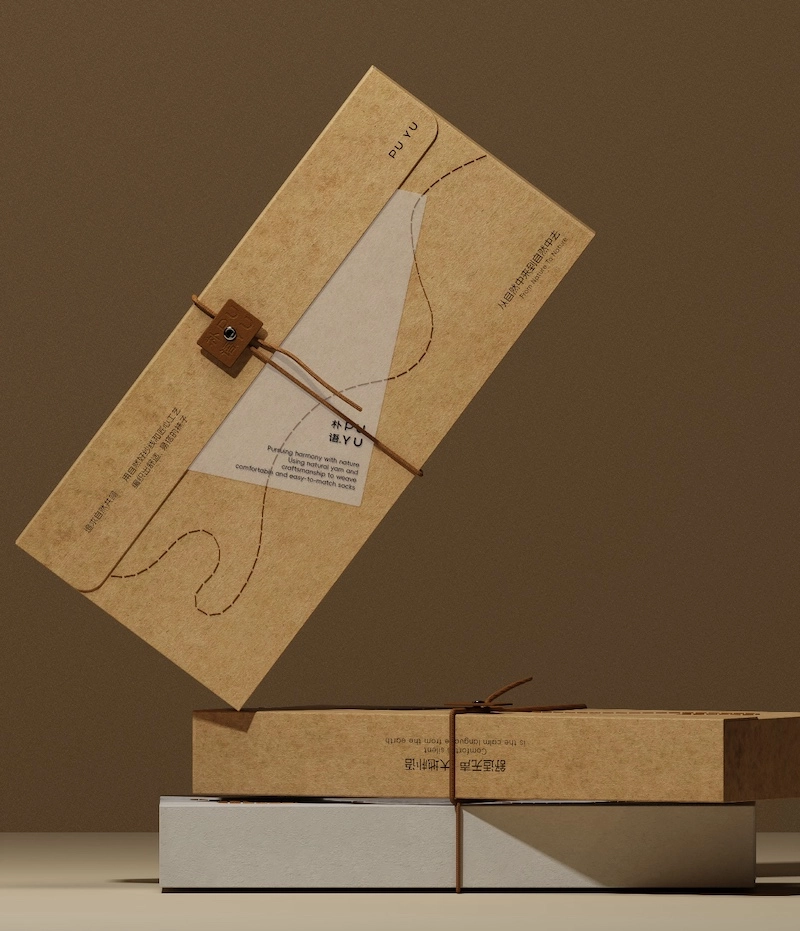
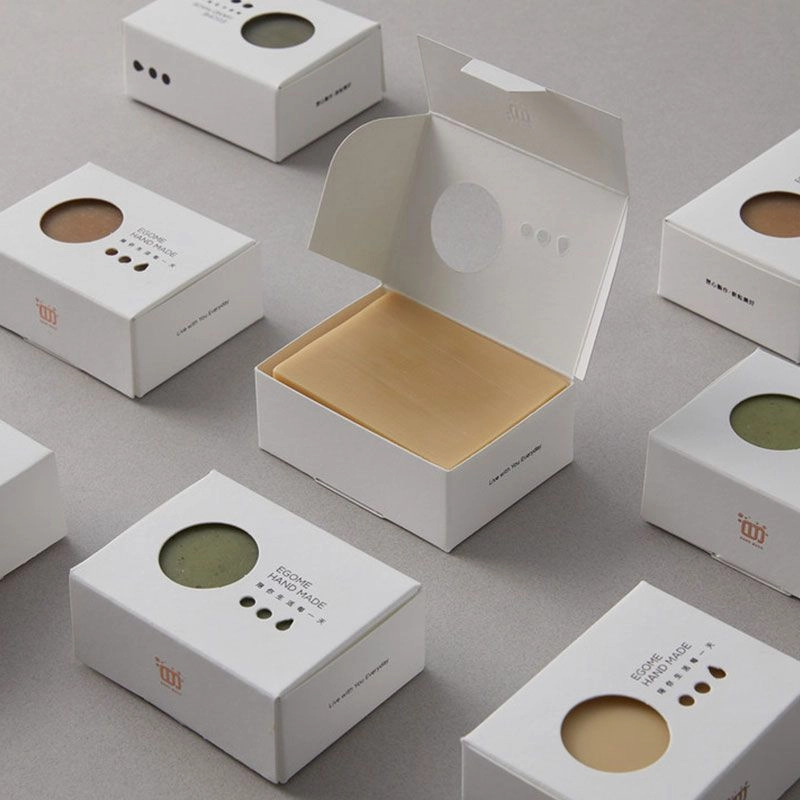
Rigid Lift-off Box
Can I order a sample of my rigid box?
Yes, we strongly recommend that you do so, we provide a variety of sample types to meet different usage situations and help you guarantee the best results!
About Us
Do you inspect the finished products?
Yes, each step of production and finished product will be carried out inspection
About Printing Craftsmanship
What is screen printing used for?
Screen printing is ideal for printing on a variety of surfaces, including:
Fabric (t-shirts, tote bags)
Plastic (bottles, packaging)
Paper (posters, packaging)
Metal and glass (signs, promotional products)
OEM Services
How long does the production process take?
Production time depends on order quantity, complexity, and customization. Generally, the process takes 7-20 days after design confirmation and sample approval. We strive for fast turnaround times while maintaining high-quality standards.
Rigid Drawer Box
What are the wholesale pricing options for bulk orders?
We offer competitive wholesale prices for bulk orders. Please contact our sales team for more details


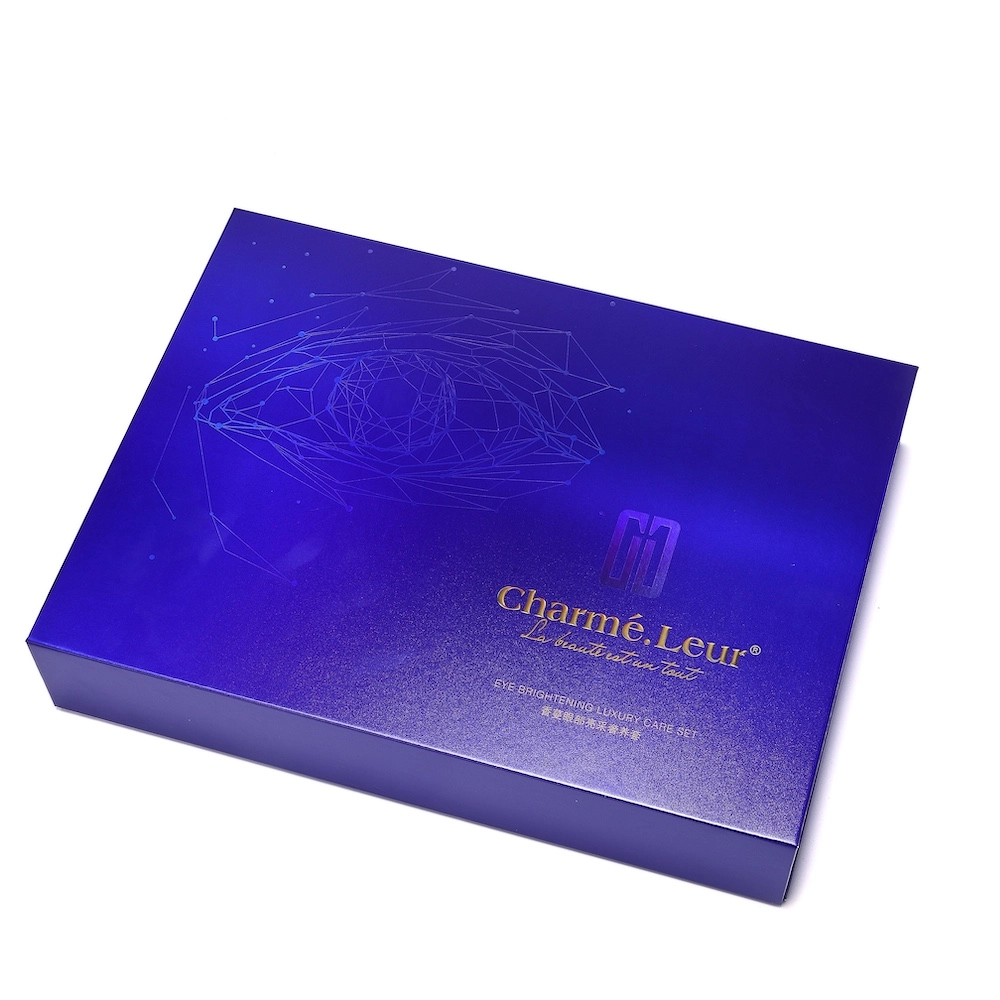

Start Your Packaging Journey Today
Discover Our Curated Collection of Bespoke Packaging Cases & Tailored System Solutions
© 2025 WINPACK PRINTING. All rights reserved
Wenhua Printing packaging
winpackprinting
Winpack Printing